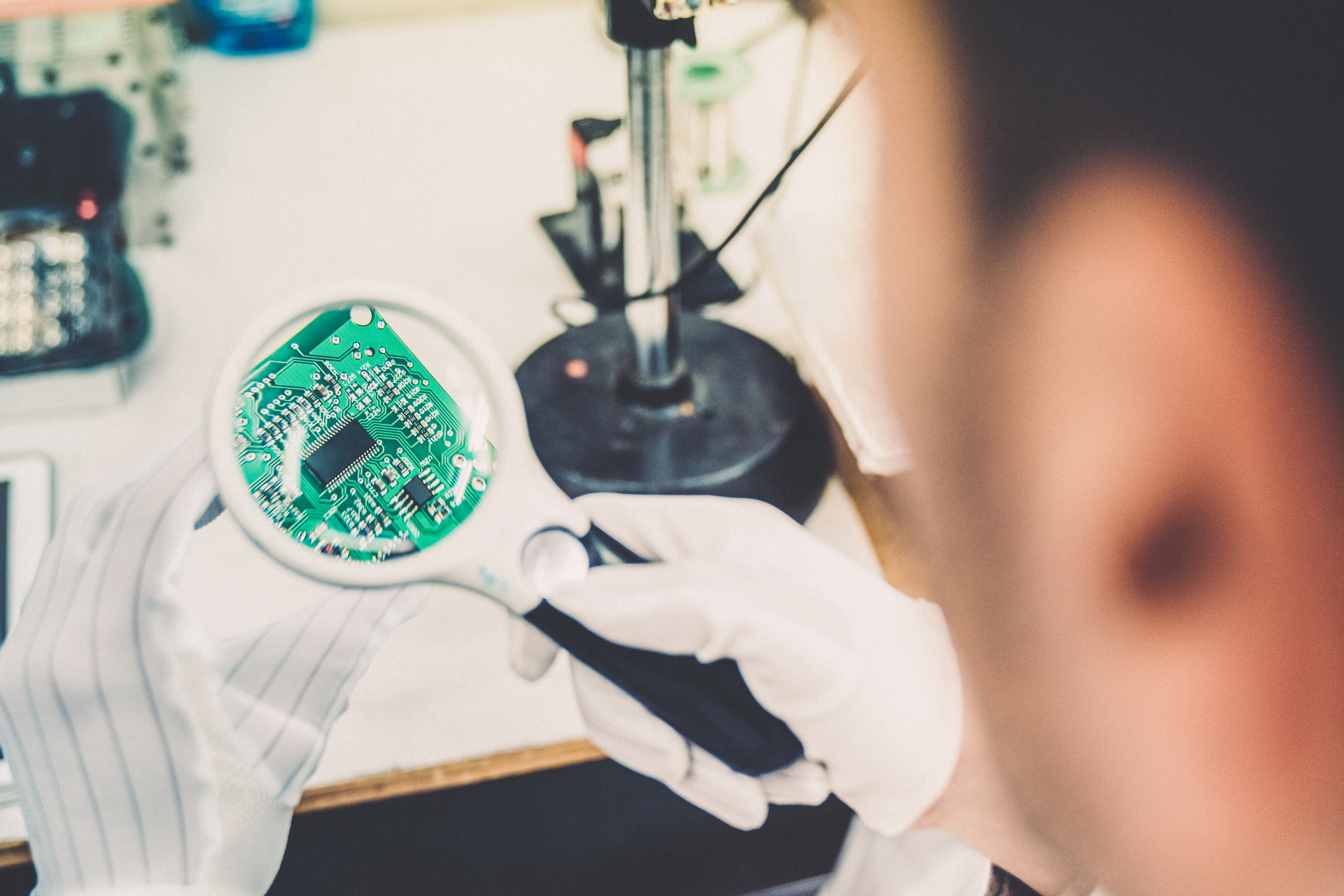
Monozukuri
Quality
Quality Assurance System
We have built a system to provide customers with safety and security.
Beginning with the design stage, we ensure high quality by checking the progress and status of quality achievement in each product development phase.
Quality Improvement
We provide high quality products that satisfy customer needs.
We enhance product quality through continuous improvement of designs, materials, and manufacturing.
Development & Analysis Center
We conduct product analysis thoroughly to improve MegaChips product quality.
MegaChips established new facility “Development & Analysis Center” in Tokyo, Japan 2022.
The “Development & Analysis Center” has the capability to analyze and investigate the products from the viewpoint of function, structure, electrical character and defect symptoms/mechanism.
We accumulate and utilize the knowledge of our analysis and investigation results to pursue further good product quality/reliability and the prevention of product defect.
In case the defect happens at customer site or market, we promise to conduct the analysis, investigation, root cause finding and prompt containment/corrective action with high priority.
Examples of Failure Analysis
-
X-ray CT Analysis Equipment
-
Observation by Microscope
-
Investigation of Voids and Cracks with Scanning Acoustic Tomography (SAT)
Product Traceability
We trace wafer, assembly, and test lots by single product marking.
An investigation of manufacturing history is extremely important when quality issues occur. Our package-marking information is managed on our system, allowing us to trace the manufacturing history of each final test (FT), assembly, chip probing test (CP), and wafer process.
International Standard
Our ISO certified quality management system follows international standards.
Standard | ISO 9001(ISO 9001:2015) | ||||
---|---|---|---|---|---|
Approved certification NO. | QC05J0270 (Registration date: March 27, 2006) | ||||
Certificate Expiry | March 26, 2027 | ||||
Certified Units | Planning, design, development, and outsource manufacturing of the following products ①System LSI products ②Communication module products and related products |
||||
Locations | Head Office: 1-1-1 Miyahara, Yodogawa-ku Osaka 532-0003, Japan | ||||
Tokyo Office: 17-6 Ichibancho, Chiyoda-ku Tokyo 102-0082, Japan | |||||
Development & Analysis Center: 2-3-8 Shinkiba, Koto-ku, Tokyo 136-0082, Japan |
Related Links